The ability to use shorter tools, improved cutting conditions and greater efficiency as a result of being able to orient the tool in the ideal direction with respect to the surface to be machined: these are the most significant advantages of 5-axis machining. On the other hand, using and programming 5-axis machines often proves to be more complex and less intuitive than with 3-axis machines. A leading builder of high performance 5-axis milling systems, Fidia has developed various specific functions to simplify their use and enable users to benefit from the advantages of this technology.
RTCP
How it works
This CNC function compensates for movement of the tool centre, owing to the rotation of the bi-rotary head, according to the angle of rotation and length of the tool. A similar operating mode is used with roto-tilting tables (ROTO function).
Advantages in 5-axis machining
- Programming of the tool centre path and feed, therefore independently of the tool length;
- Setting the tool length on the machine, so the same program can be used independently of the tool length.
Advantages in 3- and 5-axis machining
- Combined with the handwheel CQA function, manual modification of the position of one or more rotary axes during machining to avoid possible collision or improve cutting conditions.
Advantages in manual mode
- Positioning of the rotary axes by pushbutton or by the handwheel, keeping the tool centre still.
TCS
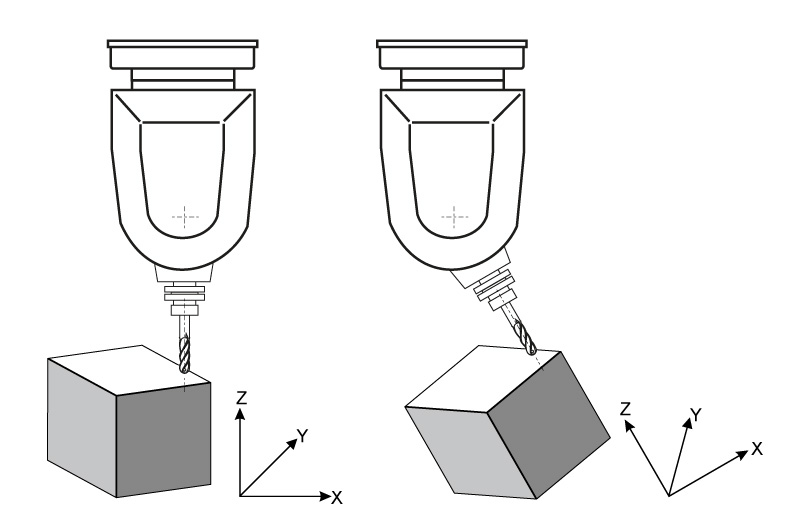
How it works
This CNC function allows the reference system to be rotated in either of two ways:
- By programming the angles of rotation and the tool centre G194 Rx Ry Rz Cx Cy Cz;
- By linking the reference system to the tool axis; in this way, when the head rotary axes are positioned, the XYZ reference system undergoes the same rotation.
Advantages
- Having performed the rotation, machining programs and axis movements by pushbutton or by the handwheel will, from that moment on, be referred to the rotated XYZ system;
- A tool path can be executed according to a reference system that is different from that used for programming; this simplifies machining programs, for example machining that is to be executed on an inclined plane can be programmed on the XY plane of the machine tool and then rotated.
Retract
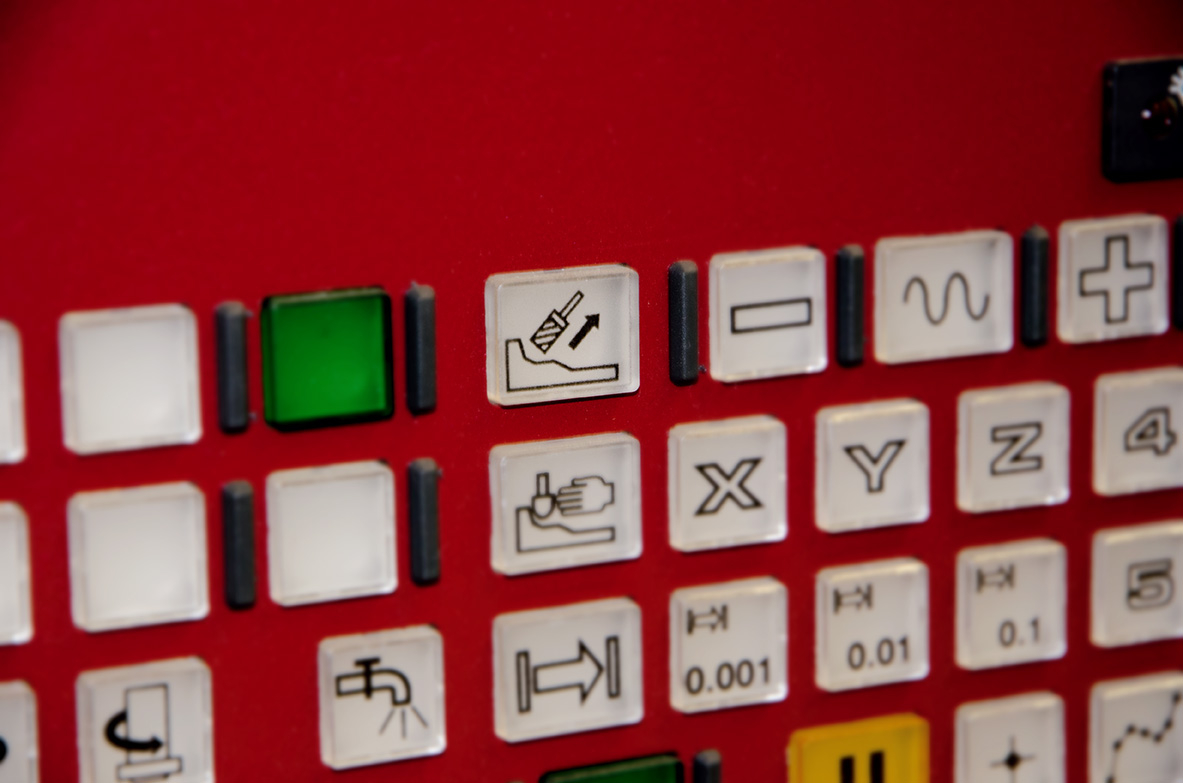
How it works
This is a pushbutton on the numerical control panel: after using the Hold pushbutton to stop the machining, pressing Retract moves the tool away from the part.
Advantages
In the event of an unforeseen interruption of the machining, the Retract pushbutton enables the tool to be moved away from the part in complete safety. This is particularly useful on 5-axis machine tools when combined with the Virtual Quill function: in this instance, the tool is moved away automatically according to the actual direction of the tool axis. When the Release pushbutton is pressed to resume machining, the tool is automatically returned to the point of interruption.
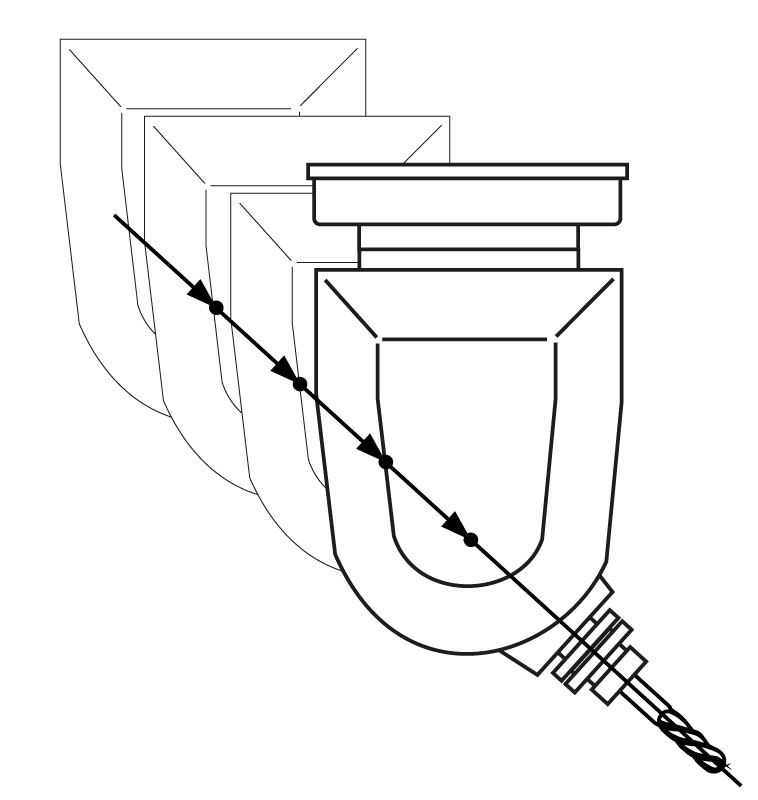
Virtual quill
How it works
This is a virtual axis, positioned according to the tool axis, that can be selected by the operator like a real axis and, also like a real axis, moved from the program, or manually by pushbutton or by the handwheel. According to the position of the two bi-rotary head axes, the control calculates the position of the tool axis and combines the X, Y and Z movement to obtain translation along this same axis.
Advantages
The virtual quill simplifies all operations in which the tool is required to move according to its axis, both manual operations and from the program, for example inclined drilling or tool release movements at the end of machining.
HMS (Head Measuring System)
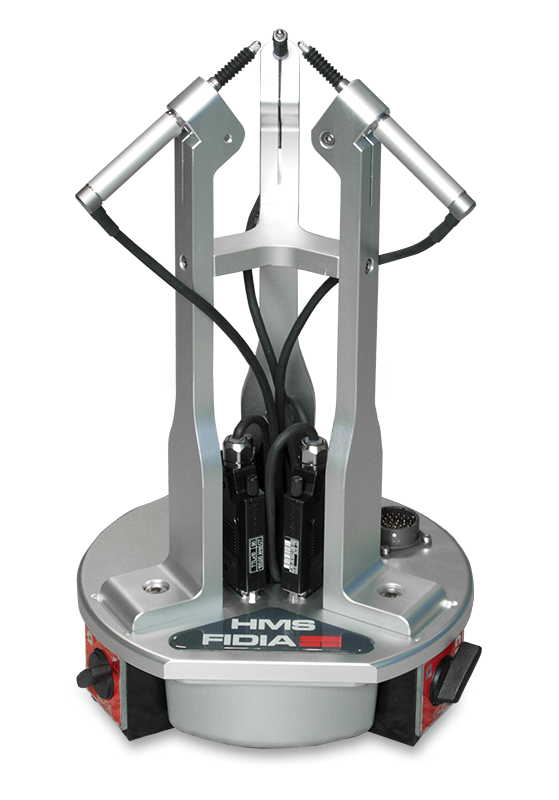
How it works
This device is used to measure and automatically compensate geometric error on continuous or indexed bi-rotary heads and roto-tilting tables. It is equipped with 3 sensors connected to the CNC and a specific measurement software.
Advantages
- Improves the accuracy and quality of machining on 5-axis machine tools;
- Can be used by non-specialist operators;
- Drastically reduces checking times compared to traditional systems (half an hour, rather than a whole day);
- Measures all head and/or table positions (not just orthogonal positions);
- Also measures RTCP parameters;
- Automatically inserts the correction values in the CNC.
Introducing the numerical control to the world of die-making more than 40 years ago, Fidia has always paid particular attention to the needs of those machining individual parts. Although tool paths are now all processed and checked on ever more reliable CAD/CAM systems, in various cases many users consider it important that a certain flexibility at the machine tool is assured, with interventions being decided by the operator according to his experience. In order to satisfy this need, Fidia has developed various specific functions.
CQA from handwheel
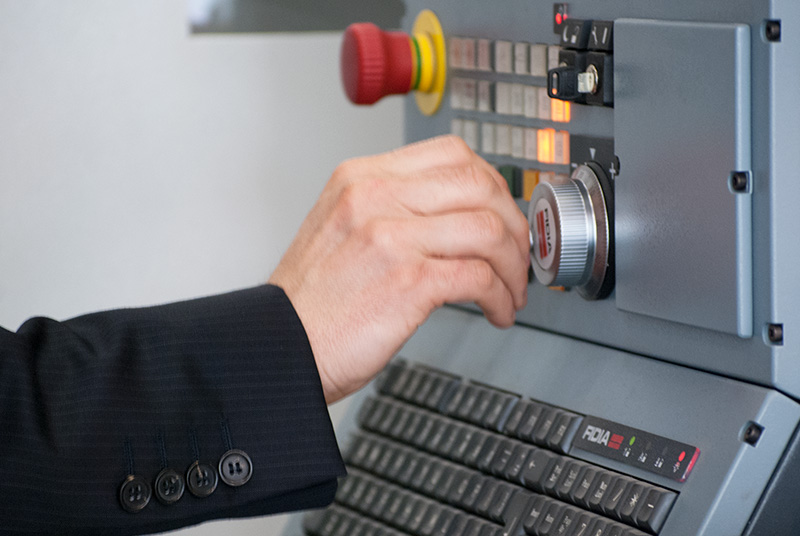
How it works
By linking the handwheel to an axis, translation along the selected axis of the machining program is enabled during program execution. All axes may be selected, including the virtual quill.
Advantages
When a machining process has to be repeated on an already machined part, in particular finishing, this function helps the operator to position the tool path. By observing the machining, the operator can use the handwheel to move the entire tool path along the selected axis in steps that are equal to the resolution of the handwheel.
ES/AP
How it works
Starting from measurements made on the workpiece by the tracer, the control calculates a new reference system aligned with the part.
Advantages
In many cases, a precise alignment of the workpiece with the machine tool reference system is no longer necessary. On the contrary, by using this cycle the control determines the reference system aligned with the part and then executes the machining in relation to it.
Trochoidal milling
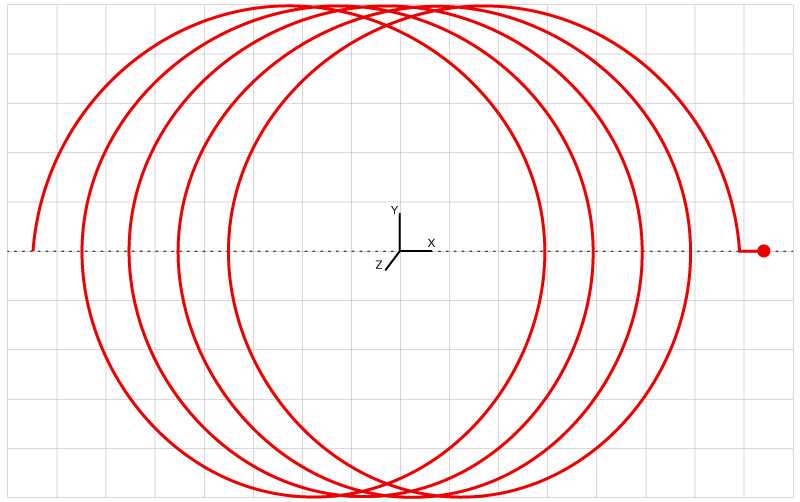
How it works
This is a milling method in which a circular movement is superimposed on a forwards movement. It is used especially for the high speed milling of slots and when using difficult materials. Specific functions enable the diameter and pitch of the trochoidal movement to be programmed.
Advantages
- Generates a reduced radial cutting force allowing for greater cutting depth
- Reduces vibration
- Smaller diameter tools can be used, reducing costs and giving greater flexibility
- Generates thinner chips and reduces the heat produced, allowing for higher feeds and cutting speeds
- Significantly increases removal rates
Dyna
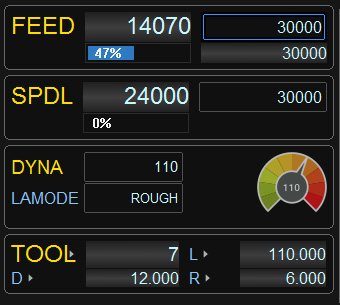
How it works
By the term Look Ahead is meant the overall algorithms governing the dynamics of the machine tool, in particular speed and acceleration, in relation to the movement of the tool path. Dyna is a parameter that acts internally on these algorithms, it is set by the machine tool operator and regulates the dynamic performance of the machine. The standard value is 100, and it can be set between 50 and 150: higher values allow for higher feeds, while lower values improve surface quality.
Advantages
It gives the machine tool operator the option of choosing high surface quality or, on the other hand, high execution speed. Being able to make this choice at the machine tool, even while machining is in progress, the operator can set the Dyna parameter in relation to the type of machining and the expected result in terms of time and execution quality. Used in conjunction with the Dyna parameter, the Lamode parameter can be set to roughing or finishing mode in order to further refine machine tool behaviour.
Predict Time
How it works
When executing a program in TP mode, the control simulates the machining and estimates the machining time.
Advantages
During execution, the control displays the end of machining time and the time remaining.